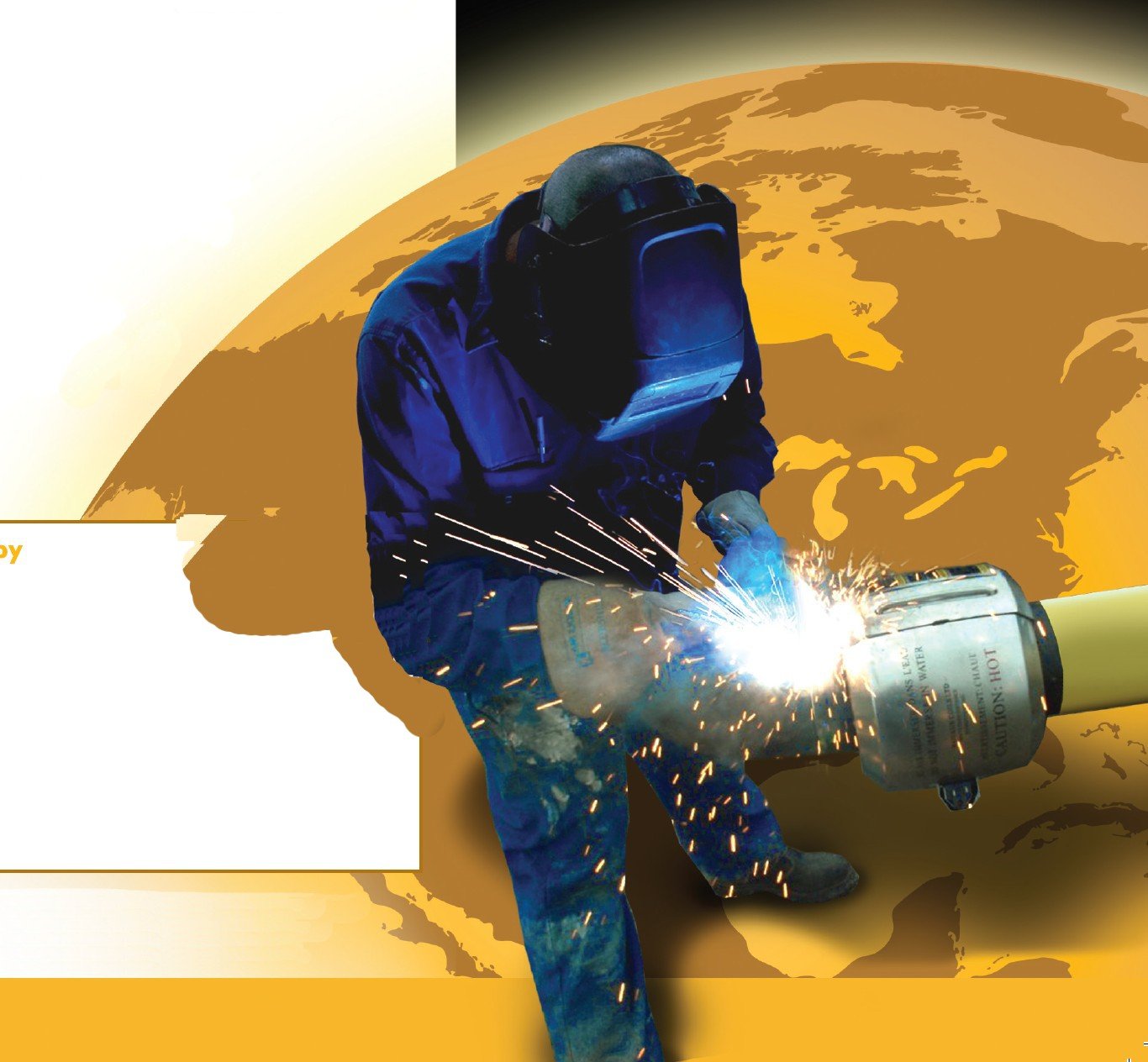
Turning Up the Heat in Firebag
FORT MCMURRAY- Suncor is just completing its Firebag Stage 3 in-situ project in Alberta Canada and Hot Coils was there to help. As part of its extensive field testing program a number of Hot Coils heaters in various sizes were used at the site to preheat pipe prior to welding.
The Firebag In-Situ Oil sands Project is Suncor’s first commercial scale in-situ venture in the Athabasca oil sands deposit. It is expected that Firebag 3 will be producing 68,000 barrels of oil per day by mid 2011.
“The Hot Coils worked out great” said the welding supervisor of the major contractor at the Firebag site who has over 20 year’s on the job experience. “They (Hot Coils) always kept us one step ahead of the job”. While welding one joint additional coils were used to preheat the next joints to be welded. This process speeds up the production cycle increasing welding productivity. “I estimate that we increased productivity over 80%”.
“In addition to increased productivity we saw an increase in weld quality” said the Piping Superintendent at the Firebag site. “When measured against weld repairs we saw an approximate 23% improvement”.
The coils adjustable thermostat with an accuracy of 2.5° easily holds the temperature to the desired specified heat helping ensure you get a good weld. “It’s important that we meet the required weld specifications and provide a good quality product” said the welding superintendent, “with the fluids these pipes handle we can’t afford a weld failure.”
The coils ability to provide even heat 360° around the pipe leaves no “cool” spots. “We find that especially in winter it’s difficult to maintain the right temperature using a tiger torch”, said the welding superintendent, “with the Hot Coils the welders could go on break and when they got back the joint was still up to temperature.”
The coils light weight, as little as 6 lbs. make them easy to handle on the jobsite. “The welding team liked that there were no propane bottles to lug around or trip over,” said the piping supervisor, “and it minimized congestion on the scaffolds making it easier for the welders to perform their work safely”. The welding supervisor added, “Unlike propane, with the coils there is no open flame, no fumes to breathe and the outside of the coils remain cool enough that you don’t have to worry about burns.”
Reliability is important; there is no time for down time on a large project like Firebag. Hot Coils were in service at the Firebag site for over 6 months. “We used them about 7-hours per shift day in and day out”, said the welding supervisor, “We didn’t baby them, the welders used them the same as any other tool. We even dropped them but they kept right on working”.
Suncor will soon begin its Firebag Stage 4 project and you can be assured that Hot Coils will be part of the production team.
Suncor is an integrated energy company which pioneered the
world’s first commercially successful oil sands operation in 1967 near Fort McMurray, in northeastern Alberta. Today, with total production nearing the one billion barrel mark and
enough reserves to sustain production for the next 50 years, the company remains a leader in oil sands development. Suncor Energy Inc. recovers bitumen from oil sand and upgrades it to refinery-ready feedstock (the raw crude oil fed to refineries for processing into transportation fuels and lubricants) and diesel fuel.
Hot Coils offer the industry a whole new technology in preheating pipe as well as in hydrocarbon bake out applications. Currently the coils are available in 4, 6, 8, 10 and 12 inch sizes that will fit standard schedule 40 pipes.
Hot Coils® a Green Technology
Hot Coils® new technology provides for highly efficient operation and the potential of saving you tens of thousands of dollars over the older traditional ways of preheating or hydrocarbon bake-out applications. The good news … while saving you money Hot Coils also makes you a better corporate citizen.
In today’s world with our increased recognition of the dramatic effects of global warming every effort to reduce our impact on the environment is extremely important. Hot Coils which operate from a common 110/120 volt power source use only minimal amounts of clean electrical energy. Electrical energy that in most part is produced from nonpolluting renewable resources such as hydroelectric and nuclear power plants.
The older traditional methods of preheating pipes such as high voltage trucks consume huge amounts of fossil fuels to generate the power required. In addition bottled gas heating systems burn large amounts of gas. That along with the burning of oil coatings or paint off the pipes surface during the flame heating process creates an unhealthy work environment for the welder. Both of these inefficient and costly methods of preheating emit high levels of CO2 and cast a very large carbon footprint on our environment.
In contrast Hot Coils reduce your costs, provide a safer, cleaner and healthier worksite while having minimum impact on our environment. With Hot Coils in your welders tool box it’s a win win situation for you and our environment.